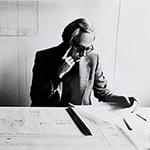
We will begin with Deiter Rams. Rams having spent over 50 years designing products at BRAUN, has developed his 10 principles of good design.
As I explore the industrial design process, through the lens of developing an ergonomic power-assisted whisk that helps people with age or injury-related mobility and pain issues engage in this simple but often exhausting cooking task, I will be applying Deiter Rams’ design principle to that process.
A product must be innovative —there has been very little to no change to the design of the whisk since Julia Child introduced it to the world in 1964. Except for attachments to immersion blenders and the whisk has remained unchanged, a static manual tool.
A product must be aesthetic, understandable, unobtrusive, honest, and as little design as possible—using simple geometry and color will allow the product to be easy to understand and operate. The simple shapes and lack of gimmicks should let it sit quietly when not in use.
Thorough down the last detail and long-lasting —this principle informs everything you do within the process. Understanding the design means spending time with it through the exploration of sketching and ideation. Only through this process can one begin to understand the product. How all the pieces fit together, what’s needed, what isn’t. How it fits in the hand, is it a couple of millimeters too large? Does it communicate with the user well? Is it effective for its purpose? When one can satisfy these questions the product has a chance at standing the test of time because a product that lasts is a product that works.
Environmentally friendly —Creating sustainable products that do not harm is more important today than ever and there is great research being done with bio-degradable bio-plastics that I will suggest being applied to my product this application would not only be a feature of the product but also vital to us all.
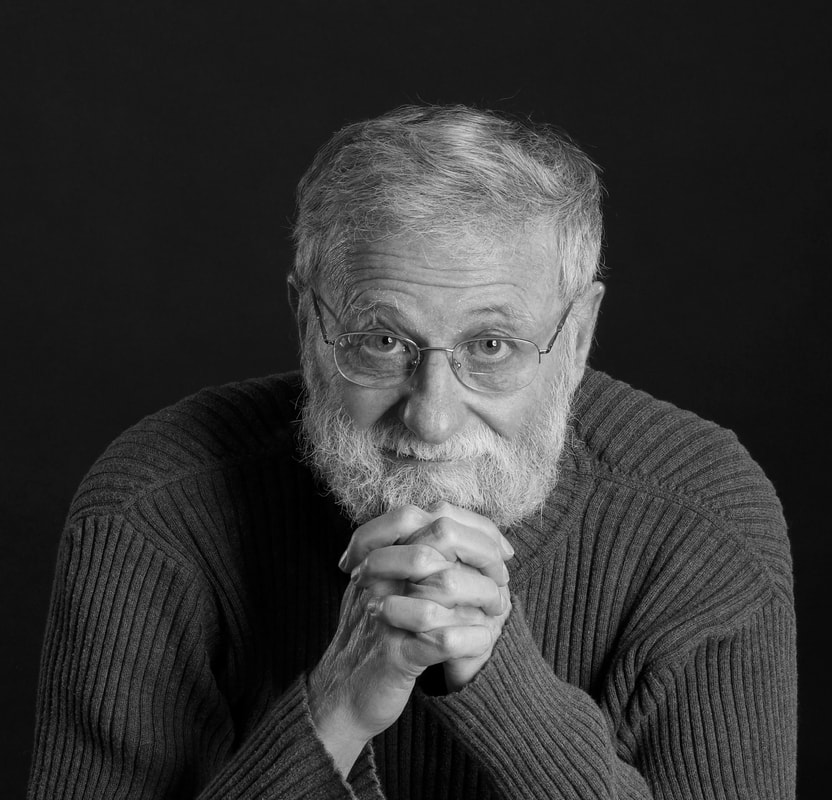
Don Norman’s Human Centered Design looks at the different ways that humans approach and think about objects. Our interactions are based on our life experience, through this training we learn how things work and what to look for to interact with objects in our environment this happens on a conscious and subconscious level. I will be using affordances, signifiers, and conceptual models for the development of my product.
Affordances —are what allow an object to function as it is intended. For example, a pencil sharpener works because there is a pencil-sized hole for the pencil to slide into to access the cutting apparatus that sharpens our pencil. The hole affords the pencil access to the blade.
Signifiers —lets us know how to interact with the object. The pencil-sized hole in the pencil sharpener signifies that this is where the pencil goes to be sharpened. If you are an alien visiting our planet and had never used a pencil sharpener you may need additional signifiers such as an illustration of the pencil in the hole. Because we are not aliens and have a lifetime of experience with the pencil sharpener we don’t need the extra-illustrated signifier. Our life experience has informed our knowledge of the pencil sharpener, we know the pencil goes into the hole without thought. This is a —conceptual model Our life experience activated from our subconsciousness tells us how to use the pencil sharpener.
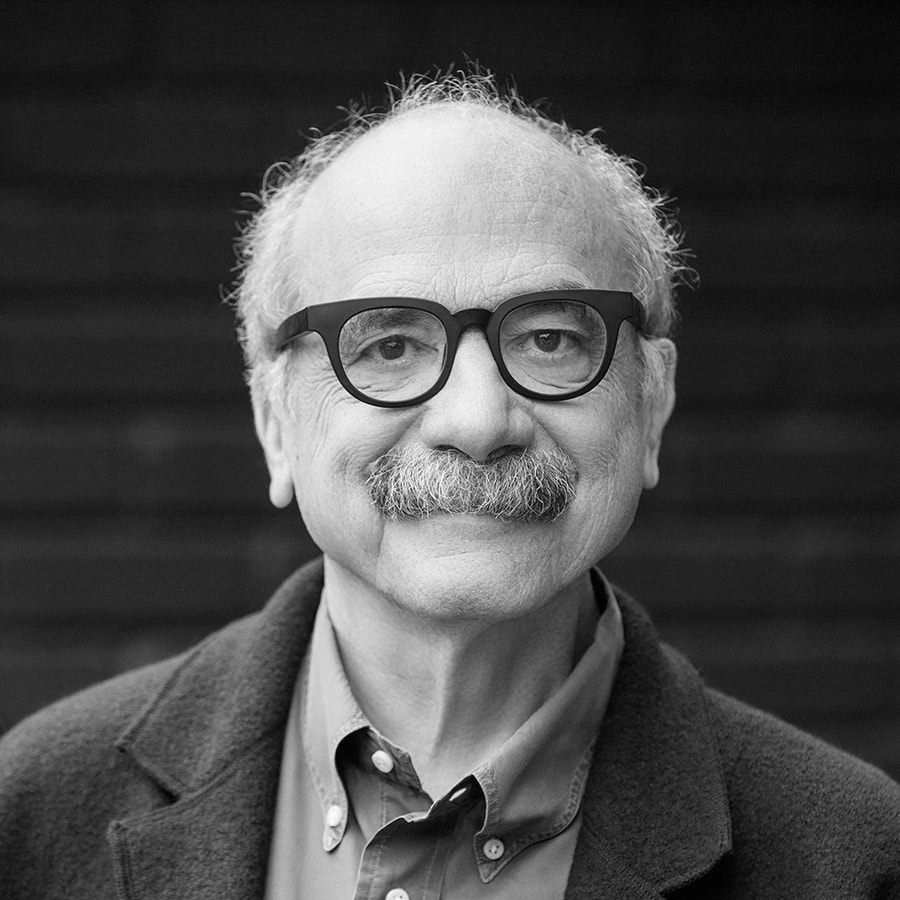
David Kelley, the co-founder of IDEO is an innovator and originator of the “Design Thinking” approach to design. Emphasizing empathy of your audience needs, quick thorough design ideation practices, and rapid prototyping.
Empathizing —taking a close look at the needs of the audience and asking questions; let us consider limited mobility, injury and chronic pain, and the task of whisking. I have learned through my research that three-quarters of the people surveyed experience pain in their hands or wrists. 80% of the same people say they would do the whisking task despite the pain or discomfort. Some questions to consider. Where is it causing problems, is it more difficult than it needs to be? Is it tiring? Does it cause pain? Learning what the existing products' pain points inform the design decisions to help create a product that is more effective easier to use and hopefully a more enjoyable experience for the end-user.
Ideation —what's another way can I do it? Come up with many ideas based on the learnings from the information gained through empathy. Here it is important to thoroughly explore even the bad ideas may in the end lead to something unexpected.
Rapid Prototyping —working in concert with ideation quickly creating a simple prototype of your product to find out if your assumptions are true —what’s working and where more attention needs to be placed. The cycling between ideation and prototyping serves to hone in on an effective functional design and one that is thoroughly considered down to the last detail.